Manage Preventative Tool Maintenance with RFID
Introduction
While using a clipboard for tool tracking might be a thrifty and somewhat productive method, tracking tools with RFID can boost productivity to greater than 99%. RFID may be a larger upfront cost than other methods, but it prevents multiple problems experienced in the workplace on a daily basis. Below are the five most common problems that tool tracking with RFID can help to prevent.
1. “I showed up to a site/surgery without the proper equipment, again.”
Whether it’s a one person construction job or a site with several trucks and employees, the proper tools are obviously required to get the job done. If an RFID mobile inventory system is installed in each work truck, an inventory count can be taken before leaving a work site ensuring no tool is left behind. Not only will it confirm that all the necessary tools are taken to a job site, but it can take a mobile inventory at the end of the day so that tools are not forgotten at the job site.
2. “The tool I’m using just broke. Looks like I can’t work until I receive another.”
One of the most common problems experienced on job sites is the lack of each tool’s usage history. Tool history provides the workers and managers with visibility into the tool’s lifecycle including hours of work, proposed next service date, and proposed end of life date. With tool tracking analytics, companies predict tools’ service dates and lifespans, ultimately saving time and money.
Currently, if a tool breaks in the field, a replacement must be ordered, which wastes employee time as they wait for the replacement to arrive. If the tool’s history had been known, the tool could have been serviced on time, or a replacement could have been ordered when the tool was near its end-of-life date.
3. “The tool that I need is lost somewhere in my truck/warehouse.”
More than likely, employees have a hard time locating the necessary tool among a sea of thousands of tools. Among all these options, different versions of tools with only minuscule differences, such as drill bit material or size, may be found making tool selection a lengthy and arduous process.
Instead of wasting time searching for a tool or potentially using the wrong tool, an RFID picking system will help employees find the correct tool and return to work in minutes.
4. “Who had that tool last? It’s missing.”
With many employees working on the same site, sometimes a certain tool is frequently in demand, which makes tracking its location very important.
A solution would be creating a check-in/check-out tool system that uses RFID tags, hardware, and software. The system gives managers visibility into not only the tool’s location, but also how long it has been there, and who currently has it.
5. “Counting inventory took three whole days. Help!”
Whether it’s a construction site, hospital, or large warehouse, inventory control can be a serious and expensive problem if thousands of tools are on hand. Managing these tools can be a full time job for some employees, which means a full time paycheck for that company.
To cut down costs and increase productivity, an RFID inventory control system can effectively manage the fleet of tools and take inventory in minutes, rather than days.
Conclusion
To learn more about specific products that aid in Tool Tracking with RFID, checkout our Tool Tracking Buyer’s Guide!
If you’d like to learn more about all things RFID, check out our website, our YouTube channel, or contact us.
To read more about RFID tool tracking, check out the links below!
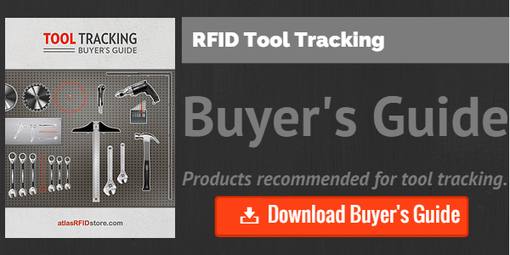