I Have an Idea for an RFID Application…
I have an idea for an RFID application. What’s next?
Many people learn about RFID and its capabilities and then think of a way this technology could benefit a business, personal, or real-world process. While RFID is useable in many types of applications, the feasibility – from either an application or cost standpoint – isn’t always there. This article walks you through the essential steps to find out if your application is RFID ready.
Step 1: What is the application?
There are two types of answers for this question - either a simple sentence answer, or multiple, paragraphs denoting specific details. While nether approach is wrong, all potential applications can benefit from spending time outlining and defining the application. Below are a few questions to consider before moving on to the next step. For more, in-depth questions, checkout Deploying an RFID System.
What problem are you trying to solve?
Who benefits from the success of this application?
How many assets/items need to be tracked?
Is there any metal or water interference?
What type of RFID is best suited for this application with regard to read range?
Do you have any specific requirements for the system (e.g. customer facing, high speed, software integration, etc.)?
Step 2: Is it Feasible?
When discussing feasibility, two distinct types should be taken into consideration - application feasibility and cost feasibility.
Application Feasibility
Will your RFID application solve the problem at hand while accommodating all the requirements outlined from Step 1? The core of determining application feasibility is understanding RFID as a technology and what it can and cannot do. In order to get a firm grip on RFID, study the basics as well as environmental issues that could arise.
Cost Feasibility
An important part of deciding whether or not to implement RFID technology is understanding the potential cost and determining if implementing an RFID system will have a positive return on investment (ROI). The ROI gauges the success rate of an application. Even if the application is successfully implemented and functioning properly, it can still be labeled unsuccessful if the cost of the system and maintenance outweigh the ROI.
Before moving to the next step, analyze the potential cost of hardware, tags, software, on-going support, etc. In order to do this as accurately as possible, learn about each aspect of a system as well as the cost of components to produce a cost analysis of the system. If the cost analysis is too high and doesn’t look like it will justify the ROI, ask for advice and accurate ranges from a company that sells RFID equipment or software. It may be possible that RFID might not be the best fit for the application.
Step 3: Talk to an RFID Professional
At any stage in the RFID process, discussing an application’s feasibility or ROI is highly recommended. Not only is RFID a relatively new technology, but some systems can have a higher price tag than others depending on the features and requirements. Don’t hesitate to discuss the application and get feedback from someone in the industry that has hands-on RFID experience. RFID professionals can help to save money and time as well as recommend the best course of action for the application. Consider them a resource.
Step 4: Testing
Depending on the advice from an RFID professional, the likely next step is to get some equipment in-house to start the testing phase.
Select RFID tags by narrowing down options based on their specifications as well as the material type and shape of the asset to be tagged. Small packs or rolls of tags, application sample packs, or mixed sample packs can be purchased for testing in order to sample a variety and ensure the best tag is chosen.
Development kits are a good way to keep costs relatively low and not over complicate the buying process while getting the necessary hardware components in-house for testing. While development kits vary, they typically include an RFID reader, one or more antennas, a small set of RFID tags, demonstration software, and access to the manufacturer’s SDK (i.e. software development kit).
At this stage, you can expect to spend up to a thousand dollars or more to begin testing. Even though purchasing RFID equipment and tags for testing may seem like a sunk cost, investing in a new technology that could potentially have a positive ROI is a risk that each company should consider carefully. Most new technology purchases begin with a risk, but investing a small amount in the beginning could result in a large payoff for a company that has a feasible application.
Step 5: Proof of Concept
After thorough testing, the next step is to develop a proof of concept for the application. This step involves using the information gathered in the testing phase to purchase and implement a minimal RFID system in the application environment. A proof of concept is used to show that the application is, or can be, successful with the chosen tags and equipment, and is frequently used to gain company or stakeholder buy-in.
Proof of concepts are usually limited to just the hardware and tag portion of the application, while software development is saved for the deployment or pilot phase.
Step 6: Get Feedback & Buy-In
Talk to stakeholders and personnel to gain buy-in by walking them through the application and proof of concept and explaining the expected ROI for the company. It is crucial to gain stakeholder and personnel buy-in, not just to receive funding for the application, but also to initiate preliminary conversations about personnel training and use of the system.
Step 7: Deploy
A pilot phase or full deployment can be rolled out after analyzing results and stakeholder buy-in have been completed. The next step would generally be to deploy the system with the hardware, tags, and any necessary software integrations. The introduction of software (i.e. scoping, development, integration, and training) can be tedious, but, because RFID has been proven successful in the application, software refinement and integration should not change the success rate.
The preferred method is to roll out a pilot phase which usually consists of a limited number of key read zones that are tested thoroughly to uncover any potential issues with the process, software, or RFID system itself. The pilot phase is a logical step between the proof of concept and a full-scale deployment with numerous read areas, and allows for any necessary adjustments before expanding the RFID deployment.
Conclusion
For a more in-depth walk through to help you decide whether your application is ready for RFID, checkout our Deploying RFID guide.
If you would like to learn more about all things RFID, check out our website, our YouTube channel, comment below, or contact us.
To read more about RFID Applications, check out the links below!
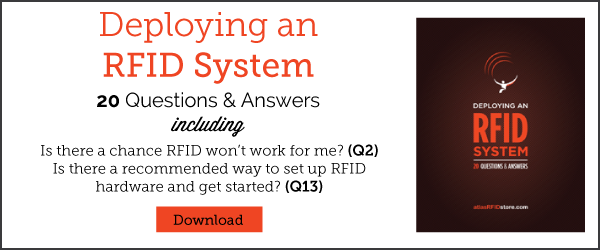